LEO TEXTILE ERP MODULES
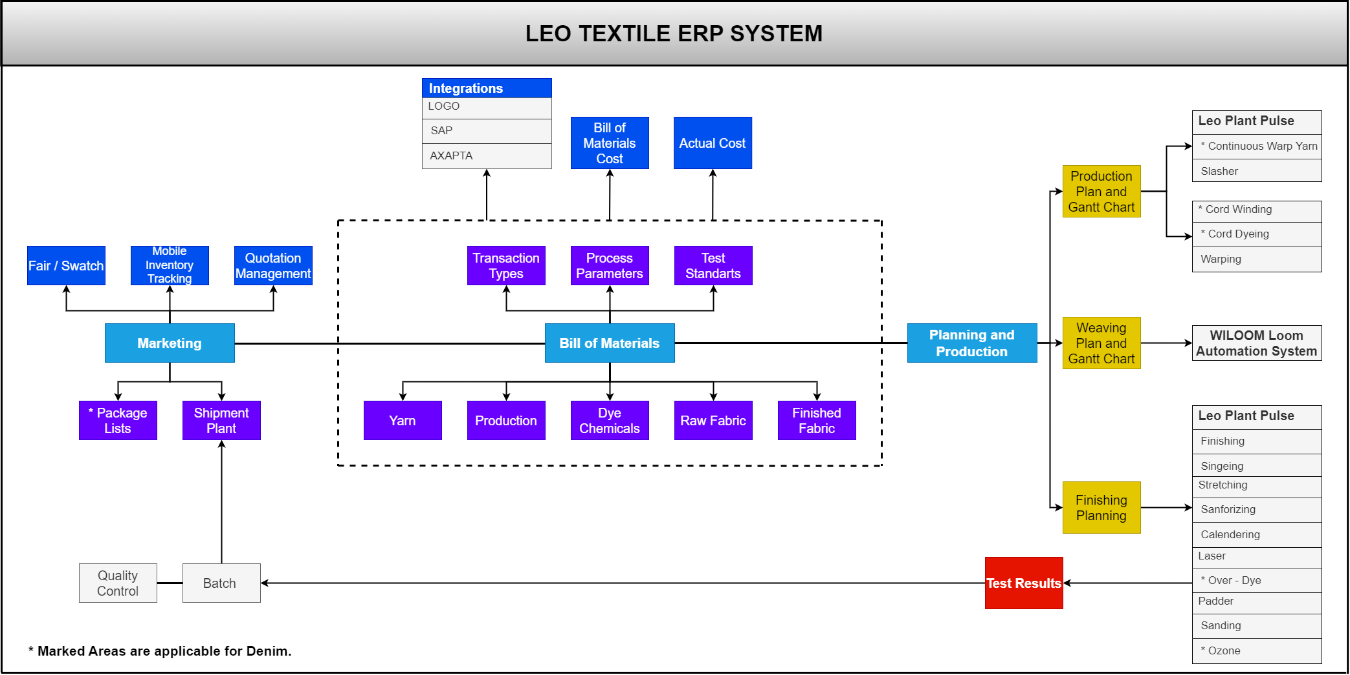
leo TEXTILE
Providing reliable, real-time information enables you to track order flow, production processes, efficiency, quality, and optimal utilization of resources, fostering a culture of continuous improvement within your business. Monitoring data that ensures the highest equipment performance and reduces losses it facilitates cost reduction and enhances your competitive advantage at a higher level.
Leo Textile features an advanced product structure system. In this system, separate product structures are created for each material where stock and production tracking is conducted, breaking down the raw materials that constitute that product (based on the product form). Furthermore, the entered values within the product structure calculate the required amount of raw materials (unit consumption) after producing the designated quantity of the textile material. A composition calculation for the final product is also performed based on the usage rates of the material’s raw components. Descriptive reports of products, naming algorithms used for identification, and additional information to be tracked beyond standard data fields can be customized according to customer requirements.
An order entry is necessary to initiate production for all production processes in the Leo Textile system. Productions are tracked based on orders. Orders managed by the marketing department undergo an approval process and are passed on to the planning department. Orders are divided and followed according to the materials to be produced. Upon entering the order for the final end product based on customer demand, orders for items that constitute the final product and can also stand alone as inventory items can be calculated and sent to the planning department’s screens for planning. Alongside the entry of finished fabric orders, raw fabric requirements and orders and yarn requirements and orders can also be generated. Based on these planning orders, the necessary steps for producing the relevant material are planned in advance or on the fly using predetermined or ad-hoc workflows. During the planning process, various analyses such as machine tracking, balance checks, deadline tracking, positions of semi-finished products in the production route, and stock controls can be conducted. Detailed field checks are performed using the work order cards provided by the system. This structure simplifies the tracking of production steps and allows for a more controlled and accurate production process, producing correct products in shorter time frames.
All production steps within the business can be tracked in detail based on the input materials and output products. These tracking processes work by the production type and are connected to the main program, Leo Textile. To ensure that production tracking is closer to actual operations, the required amount of raw materials to be produced must be available in the intermediate warehouse of the relevant production process. Additionally, various calculations subject to analysis, such as production time calculations, are made during production. This allows relevant departments to assess their work efficiency. The production module in the system mainly maintains analysis data of production notifications made through auxiliary programs and presents reports generated based on these analyses according to customer demand.
The stock tracking for every material recorded in the product tree can be managed through Leo Textile. The entry of these stocks into the warehouses can occur through procurement or production notifications within the system. The warehouse structure can be examined under two main categories: main warehouses and intermediate warehouses. Main warehouses are the form of warehouses where stocks are separated according to the smallest units and maintained under a single barcode. Among these warehouses are various processes such as transfer operations and warehouse addressing. Intermediate warehouses, on the other hand, hold batches of barcodes in bulk, and these warehouses are used for tracking the consumption of raw materials based on the production orders when production notifications are made in the system. The consumption is done from the specified batch of products. Inventory tracking is one of any business’s most essential and challenging tasks. However, with Leo Textile, warehouse management includes the management of requests and transfers between warehouses as per customer demand, control of required consumables, and various checks with tolerances. Labeling the stocks and designing these labels are also adjusted according to customer demand.
Within the business, you can minimize the time spent searching for products within all depots by individually defining all depots, their locations, shelves, rack slots, floors, and information such as pallets, boxes, and sacks. You can view and report the status of products in barcode or bulk (e.g., lot) in depot screens. You can carry out transfers of products between warehouses in a planned or unplanned manner and obtain transfer lists for shipments to different locations. You can regularly confirm stocks with counting processes. You can perform transfer operations with RFID, standard barcode readers, or handheld devices. Bulk operations for packaging or pallets are also supported.
Features include:
- Raw material, Main Warehouse, and Finished Goods Warehouse tracking
- Purchase Entry and Return
- Outsourced Production Raw Material Transfer
- Outsourced Raw Material Tracking
- Outsourced Production Warehouse Entry
- Products, Lot (Purchase/Outsourced Production/Production), Packaging (Pallet/Box/Bag, etc.), Quality (Production Quality Classification), Customer, Order, Work Order, and warehouse breakdown
- Warehouse details by date
- Business Raw Material Request structure
- Business Raw Material Transfers-Returns from Production
- Business-to-business raw material transfers
- Special transfer methods between productions
- Dye/Chemical Lot Tracking
- In-house Solution Tracking
- Internal Repair Warehouse Management
- External Repair Warehouse Management
- Shipment Preparation Warehouse Management
- Buffer Warehouse Management
- Raw Material and Finished Goods Warehouse allocation and reservation
- Shipment Warehouse Customer Risk Management and shipping controls
- Production and Warehouse Equivalence structures
- Inventory tracking
Dyeing and finishing productions form a comprehensive structure that begins with Raw Yarn, Warp, or Raw Fabric, continues with finishing processes, and concludes with quality control efforts. This scope is possible for businesses with route definitions tailored to their product variety and utilized materials.
Different production programs can be used based on the defined routes’ included processes and/or preferences. While the applied processes may differ among companies, LeoTextile, due to its accumulated expertise, offers a variety of programs capable of implementing all dyeing and finishing processes.
For specific pre-finishing tasks such as batch preparation and transfer, programs compatible with handheld devices (palm devices) can be used, and the process can also be executed on a computer. Depending on the applied process, an online data application like LeoPulse or different programs can be employed for dyeing and finishing processes.
Production tracking and planning interventions are provided through the LeoTextile management program for dyeing and finishing productions. Some processes that require meticulous tracking (Dyeing Machine, Finishing, etc.) can utilize Workload (Gantt) screens, allowing interventions such as machine assignments, planned quantities, sequence changes, and recipe allocation to be performed.
In addition to having its own Dye/Chemical weighing program, LeoTextile can also integrate with third-party dye weighing and dosing programs. This facilitates production management and controls through a single program, and dye and chemical consumption can be tracked.
The Dye Laboratory module encompasses the processes involved in creating recipes for dyeing processes used within the facility.
Primarily covering pre-treatment, dyeing, and post-processing recipes, the recipe definitions obtain dye and dye auxiliary chemicals from color recipes used during the dyeing process. Color recipe efforts are tracked using the Laboratory Management System (LMS). In conjunction with other recipes, the color recipe resulting from the LMS process forms the batch recipe.
Initiating customer orders, internal orders, or laboratory orders created for testing purposes, the LMS process enables the efficient tracking of all stages up to the approval of the color recipe. Generally, the LMS includes processes such as Laboratory Order, Laboratory Planning, Pipetting Integration (Optional), Laboratory Production, Tube Approval Processes (Unit and Customer Approval), and Color Recipe/Color Code Generation.
Within the system, opportunities exist for conducting tests on materials that undergo stock entries (purchased or received from outsourced production), samples, and materials acquired from production in real time. The testing process begins with responsible parties defining various aspects. These encompass applied test types, utilized testing methods, and the consolidation of tests applied to the same material using test packages. Subsequently, users enter test results for various test types (stock entry, sample, and production) through separate screens and record their outcomes. As previously defined in test packages, the minimum and maximum values required for a specific test’s acceptance are input, allowing the system to calculate the test result automatically. Depending on customer preference, this result is then confirmed by the operator. Similarly, the system can automatically generate tests such as stock entry or production testing and only require operators to input the results. This module also enables the creation of analysis screens and reports regarding test outcomes. Businesses equipped with the laboratory module can halt the entry of products that do not meet the desired test results into the facility or prevent their shipment from the facility to customers using systematic controls.
Leo Textile offers both raw fabric quality control and finished fabric quality control. These processes are conducted through auxiliary programs integrated with the main system. Utilizing meter counters connected to inspection tables, the system tracks the progress of the fabric in meters simultaneously with the fabric on the inspection table. Moreover, automatic data acquisition from scales significantly reduces the workload on operators. Alongside more straightforward quality control options, the system provides more advanced quality control alternatives for finished fabric, including optimized and non-optimized quality control based on customer quality standards. Since the entire system is consolidated under a single program, quality control processes can seamlessly integrate into workflow processes without integrating with other programs.
The shipping module enables you to prepare products from your finished goods inventory for shipment, allowing for expedited processes during barcode scanning and list preparation at the time of shipping. You can create package lists to accelerate barcode scanning and list preparation during shipping. Shipping lists can also be modified to accommodate changes in orders or customers. The planning or marketing departments can prepare shipping orders for the shipping unit, ensuring that shipments are carried out organizationally. Using handheld devices for barcode scanning or RFID label scanning helps prevent incorrect shipments. Customized outputs such as packing lists, customer barcodes, and other documents can be designed based on customer requirements. The generated invoices can be seamlessly integrated with accounting software. The module facilitates vehicle planning for shipments to different addresses and enables efficient capacity utilization. The configuration of shipping processes can be tailored to your company’s workflow through parameter settings.
Within Leo Textile, the Standard Cost module enables the modeling and period-based tracking of textile products and production parameters throughout all stages.
The Actual Cost module makes detailed tracking of production costs across all stages, from initial input to the final finished product possible. Direct and indirect expenses are generated based on cost centers with all account breakdowns integrated with accounting. The detailed inventory structure calculates costs parametrically for raw materials, plant, and finished goods inventory. Subcontracting costs and subcontracted production structures are reflected in actual prices.
The Pre-Cost module allows for the creation of customer-specific price quotes with detailed cost information. Cost details are generated using reference products, enabling dynamic and rapid cost calculations based on parameters like raw materials and production calculations.
The Customer Price List module enables the creation of flexible price lists for products with established standard costs, based on dynamic calculation methods tailored to individual customers. During Customer Order entry, analyses of cost and profitability can be conducted using the Price Lists.
Fair & Hanger module tracks and analyzes every step of sample fabric and Hangers, from the production process to customer delivery.
- Unlimited user profiles can be defined.
- Screens can be authorized on a user basis.
- Data can be exported from analysis screens to Excel.
- Products and all sub-products (colors, variants) can be managed from a single screen.
- Product and washing instruction images can be uploaded to the system.
- Group hangers can be created by selecting different products.
- Hanger and sample orders from customers can be quickly entered into the system, and detailed order status tracking can be done. Additionally, order details can be automatically recorded by the system during shipment.
- Barcodes can be printed for each produced hanger, and detailed production tracking can be done.
- The system can work with all barcode printers and label design can be done according to requested dimensions.
- Real-time tracking of hangers and sample fabric inventory is possible.
- Barcode-based inventory tracking is available.
- Hanger and sample fabric shipments can be made based on orders, and detailed shipment analysis can be accessed on the screen.
- Shipment packing lists can be obtained and, if requested, saved in PDF format and sent to customers via email.
- Analysis reports for all operations related to hangers and sample fabrics (order, production, inventory, shipment, and trade shows) can be accessed through the system, and reports can be customized based on requests.
- Companies that track hangers and sample fabrics conduct on-site analyses with relevant departments, and based on the analysis, the most suitable project proposal is presented to the company.
The application is based on two main aspects: Planned and Breakdown Maintenance, designed to prevent potential failures in the operation of the company at specific intervals and to address unexpected failures that occur.
Through the application, both Planned and Breakdown Maintenance can be defined. Instructions, materials, and resources related to these defined maintenance tasks can be added. Work orders can be generated for the defined maintenance tasks. Automatic stock deductions are made for the entered materials.
Key features supported by the Maintenance Application:
- Maintenance Planning and Management: Managing the planning and execution of planned maintenance activities.
- Breakdown Maintenance Management: Handling unexpected breakdowns and repairs.
- Resource Tracking: Keeping track of the resources required for maintenance tasks.
- Consumable Material Tracking: Monitoring the usage of consumable materials during maintenance tasks.
- Spare Parts Procurement Tracking: Managing spare parts and auxiliary materials procurement activities.
- Downtime Tracking: Recording downtime periods for each machine during both planned and breakdown maintenance, enabling the tracking of production losses on a machine and department basis.
- Execution of Planned Maintenance: Conducting planned maintenance tasks according to standardized instructions.
- Cost Tracking: Keeping track of costs related to breakdown maintenance, planned maintenance, and outsourced services.
The Maintenance and Repair application helps ensure machinery and equipment’s smooth operation by systematically performing preventive (planned) and corrective (breakdown) maintenance tasks. It offers features to streamline the maintenance process, track resource utilization, manage spare parts, and monitor downtime, all of which contribute to optimizing the company’s overall operational efficiency.
Request Management:
- Centralized View: All requests can be viewed on a single screen. Different authorization levels can be set for request approval, and operation requests from different locations can be tracked from a central point.
- Approval Workflow: Requests with different authorization levels can go through an approval process.
- Request Analysis: Analyze request quantities and fulfillment rates for different company units.
- Conversion to Quotations or Orders: Requests can be turned into quotations or direct purchase orders.
Quotation Management:
- Creating Quotations: Quotations can be generated from registered suppliers or based on requests in the system.
- Comparison and Selection: Quotations can be compared in the system, and orders can be placed based on the most suitable quotation.
- Quotation Analysis: Track which units’ requests generated quotations and which quotations turned into orders.
Order Management:
- Order Creation: Orders can be generated based on requests for quotations, or by entering supplier, payment method, quantity, price, etc.
- Order Form: The system can email the order form to the supplier.
- Order Tracking: Monitor order quantities, delivery dates, and returns.
- Source Information: Easily find out which requests or quotations the orders are based on.
Approval Structures:
- Customizable Approval Flows: Define approval flows for requests, quotations, and orders specific to different units.
- Delegation of Approval: Authorization can be delegated.
- Special Approval Levels: Custom authorization levels can be established based on quantity and price.
Reporting:
- Generate reports based on department, staff, purchasing manager, budget category, date, product, and supplier.
Contract Management:
- Contract Uploading: Fixed quantity and date-based contracts can be uploaded into the system. Orders can be created based on contracts. Contract validity can be tracked historically.
Integration with Receipts and Inventory:
- Goods Receipts: Receive goods based on purchase orders, track returns, and manage related documents.
- Delivery Note Handling: Perform necessary delivery processes within the system.
This module streamlines the procurement process, from generating requests, managing quotations and orders, and tracking approvals and contract management. It provides a comprehensive solution for efficient procurement operations within the organization.
Through integration with ERP modules, customer order management allows for easy and quick order entry and real-time tracking of production and shipment statuses. When entering orders, you can select customer details, shipping company information, billing company information, payment method, delivery method, and freight details for various complex order scenarios.
Key Features:
- Flexible Order Entry: Easily input various order details, including customer selection, shipping and billing information, payment and delivery methods, and freight details.
- Integration: The module integrates with other ERP components, providing a comprehensive view of order-related processes.
- Complex Scenarios: Handle complex order scenarios with different combinations of options, ensuring an accurate representation of customer requirements.
- Approval Mechanism: Collaborate with the planning unit to determine shipment deadlines based on existing workloads. Use an approval mechanism to ensure accurate shipment terms.
- Real-time Tracking: Monitor production progress and track current customer balances in real-time.
- Automated Notifications: Utilize the system to automatically send notification emails, keeping customers updated on their order’s progress.
This module enhances your order management process, providing a centralized platform to manage order entries, production, and shipment statuses, resulting in streamlined operations and improved customer satisfaction.
Sustainable Raw Material Management (INPUT):
- Management of Organic and Recycled Fibers and Yarns: Systematically manage whether fibers and yarns are organic or recycled.
- Recording Document Numbers for Raw Material Stock Entries: Record document numbers for incoming raw material stocks.
- Management of Sustainable Certified Materials in the Warehouse: Manage the warehouse of sustainable certified materials.
- Supplier-Certificate Management for Sustainable Materials: Manage suppliers’ certificates for sustainable materials.
- Transparency in Raw Material Evaluation: Evaluate suppliers based on transparency principles.
- Sustainable Document Management: Manage documents related to sustainability.
Sustainable/Traceable Process Management (PROCESS):
- Eliminating Potential and Actual Risks from Supply to Production: Monitor and eliminate potential and actual risks of materials from the supply stage.
- Real-time Water and Wastewater Monitoring System via ESIS Integration: Monitor real-time water and wastewater through ESIS integration.
- Chemical Pollution Monitoring: Monitor chemical pollution loads of fabrics on a batch basis via OrgaTEX integration.
- Dyeing and Finishing Production Monitoring with LEO PULSE IOT Solution: Monitor dyeing and finishing production with LEO PULSE IOT solution.
- Chemical Standard Compliance: Track compliance of chemicals with standards like Oeko-Tex, Eco Passport, ZDHC MRSL, GOTS, etc.
- Weaving Production Monitoring with Wiloom IOT Solution: Obtain sustainable production indicators through the Wiloom IOT solution.
- Control of Hazardous Material Usage: Control the use of hazardous materials according to sustainability principles.
- Tracking Products with Hazardous and Restricted Components: Track products containing hazardous and restricted components.
This module supports the monitoring, management, and adherence to sustainability standards from raw material to product in line with ZDHC’s clean production principles.
Management of Inventory Containing Hazardous Components (OUTPUT)
ZDHC Reporting:
You can obtain Chemical Discharge Rates, Chemical Consumption Analysis, Chemical Compatibility Analysis, and Chemical Consumption Positive List daily/monthly and yearly through the LEO Textile application.
ZAMAN AŞIMINA
UĞRAMAYIN
Nemo enim ipsam voluptatem quia voluptas sit aspernatur aut odit aut fugit, sed quia consequuntur magni dolores eos qui ratione voluptatem sequi nesciunt. Neque porro quisquam est, qui dolorem ipsum quia dolor sit amet, consectetur, adipisci velit, sed quia non numquam eius modi tempora incidunt ut labore et dolor.
Nemo enim ipsam voluptatem quia voluptas sit aspernatur aut odit aut fugit, sed quia consequuntur magni dolores eos qui ratione voluptatem sequi nesciunt. Neque porro quisquam est, qui dolorem ipsum quia dolor sit amet, consectetur, adipisci velit, sed quia non numquam eius modi tempora incidunt ut labore et dolor.
Nemo enim ipsam voluptatem quia voluptas sit aspernatur aut odit aut fugit, sed quia consequuntur magni dolores eos qui ratione voluptatem sequi nesciunt. Neque porro quisquam est, qui dolorem ipsum quia dolor sit amet, consectetur, adipisci velit, sed quia non numquam eius modi tempora incidunt ut labore et dolor.
Nemo enim ipsam voluptatem quia voluptas sit aspernatur aut odit aut fugit, sed quia consequuntur magni dolores eos qui ratione voluptatem sequi nesciunt. Neque porro quisquam est, qui dolorem ipsum quia dolor sit amet, consectetur, adipisci velit, sed quia non numquam eius modi tempora incidunt ut labore et dolor.